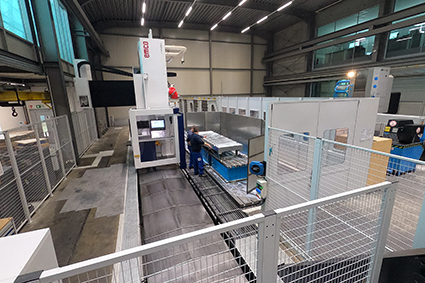
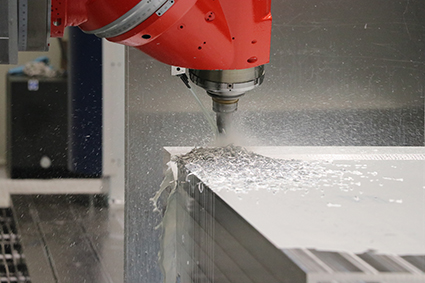
Mecmill maximises precision and productivity
Founded in 1963, Grunewald is a medium-sized company with around 200 employees, now managed by brothers Ulrich and Philipp Grunewald. The company specialises in the development, design and production of lightweight metal parts and plastic components, as well as the construction of innovative tools and moulds for demanding sectors such as the automotive and aerospace industries. Grunewald faces the challenge of maintaining high quality under severe cost pressure, especially due to low-cost competition from Far Eastern countries, which often produce moulds of inferior quality, requiring costly rework.
Grunewald does not compromise on quality, and therefore does not participate in aggressive price competitions, but instead focuses on quality products for long-term success. It faces cost pressures with modifications that ensure the optimal functioning of its moulds and tools. The key to their success is experienced and qualified employees, supported by local partner companies, who cover the entire value chain from design to production and quality assurance. They use modern technology, including a new Mecmill milling machine from Emco Mecof, capable of producing large moulds and tall tools, significantly improving their production capacity.
High flexibility with a moving column machine and pendulum machining
Grunewald chose a moving column machine instead of a gantry machine because of the larger machining area available in the same space and the flexibility offered, especially in height and angle milling. The decision to purchase the Mecmill from Emco Mecof was influenced by the good value for money and the positive past experiences with the company, starting in the 1990s. The old machine, an M 5.3, while reliable, was no longer adequate for the new demands of quality and precision. The new Mecmill was able to utilise the existing foundation and milling table, reducing costs and installation time. The order was placed in May 2021 and the machine went into operation at the end of September 2022.
Ulrich Grunewald confirms the soundness of the decision to buy the Mecmill, only regretting that he had not done so sooner, given the 30% energy savings. The machine, operating in two or three shifts, allows considerable savings due to its high level of automation, which enables unmanned night shifts. Jörg Engler points out that employees set up long finishing operations at the end of the shift, taking advantage of the automatic tool magazine and head change to run programmes during the night or weekend. The Mecmill guarantees high precision and surface quality, achieving an accuracy of 7.5 cents on curved surfaces and a quality of Ra = 0.8 μm in fine finishing. This reduces the time needed for polishing, improving overall efficiency.
In addition, the pendulum machining of the new Mecmill milling machine reduces unproductive time, allowing operators to prepare new components on one side while the other is running. This milling machine is highly manoeuvrable and efficient, with CNC programs transferred directly from 3D CAD to the Heidenhain TNC 640 HSCI control. The operators set up the machine, clamp the blank and start the production process, monitoring it especially during heavy roughing. Despite initial slow problems with some plates, the Emco experts quickly optimised the settings, confirming Emco's positive service experience.