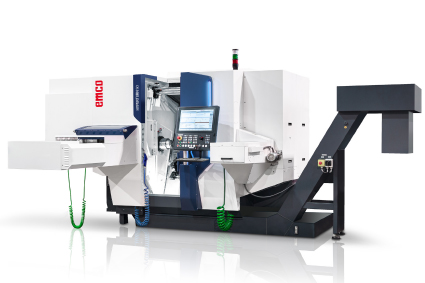
Equipped with a Bigbore 51 spindle as standard, the Hyperturn 50 has a larger bar capacity for greater flexibility in bar machining. In addition, the drive power of 8.8 kW and 12,000 rpm allows powerful milling operations, even in demanding steel materials. Naturally, the Hyperturn 50 also features state-of-the-art control technology from FANUC with the FANUC 31i-B Plus or Sinumerik ONE, both with EMCONNECT user interface. The HT50 can be automated either with various bar feeders or with an EMCO swivel loader, EMCO gantry loader or the Robojob Turn-Assist for piece feeding.
The HYPERTURN 50 impresses with a large spindle distance of 760 mm for collision-free machining with two turrets. The extended working area offers sufficient space for the integration of BMT turrets in 12- or 16-position versions. With the precision interface for fast set-up and the direct drive for high-performance milling of complex workpieces, this option is the first choice. The water-cooled direct drive delivers 8.8 kW, drills and mills at up to 12,000 rpm and enables 20 Nm torque. The stable and precise BMT interface guarantees a long tool life. All in all, the user has more options for machining workpieces and increasing productivity.
Machine design
The 72° inclined bed forms the core of the machine. Designed as an extremely rigid and compact welded steel construction, it forms the basis for a robust and precise lathe. Reinforcements provide additional rigidity in areas subject to higher stress. The use of steel instead of conventional machine casting offers advantages in terms of rigidity and the thermal behavior of the lathe during the warm-up phase. All guides are designed as preloaded roller guides. These are screwed onto precisely machined support surfaces and sealed with spring steel cover clips to prevent contamination. Fixed stainless steel covers in the working area increase operational safety and service life.
Main spindle/counter spindle
The high drive power of the spindles, combined with optimal torque, ensures operational productivity when cutting steel and cutting aluminum at high speed. Integrated spindle motors (ISMs), equipped with large high-precision bearings make it possible to achieve exceptionally high rotation speeds, coupled with extremely good true running characteristics.
Symmetrically-designed spindle stocks combined with temperature sensors on the bearing points and liquid cooling ensure high thermal stability.
In the HYPERTURN 50, the counter spindle is mounted on a linear roller slide and can travel over a distance of 510 mm. A parts ejector with stroke monitoring and cooling ensures the finished parts are safely placed on a conveyor. On request, the clamping cylinder without through-hole can be replaced by a hollow clamping cylinder with a 45 mm diameter through-hole for removing long slender parts through the counter spindle.
Using the latest control and drive systems by Siemens / Sinumerik ONE, or Fanuc 31i-B Plus, both of which also come with EMCONNECT, the machine can be programmed in a straightforward and effective way. The new height-adjustable and rotatable operating panel offers extraordinary ergonomics, especially during prolonged programming work. An innovative, multi-colour LED status bar has been integrated into the machine cladding so that the operator can always keep track of the current machine states.
EMCONNECT
A digital process assistant for the comprehensive integration of customer- and system-specific applications for controlling the machine and the production flow, EMCONNECT interlinks and networks the production environment. In order to create more efficient work processes without losing sight of the machines' outstanding reliability in all operating modes, the operating sequences focus on the user and their requirements.
With EMCONNECT, users can access important additional features directly via the control panel, which means that it is possible to access all important details, data and systems directly and centrally at the machine. EMCO's modular system makes it possible to implement even project- and customer-specific applications in an extraordinarily flexible way. Thus, EMCONNECT is the key to ideal work processes and increased productivity.
The range of available apps is continuously being expanded. As of now, for example, you may download our Option Shopfloor Data for the collection of machine and operating data. It ensures comprehensive monitoring of all machines as well as process organisation in the production area. This product is characterised especially by machine and manufacture independence and mobile access to the machine state using a smartphone or tablet PC.
In order to minimise machine downtimes, we are currently developing the EMCONNECT Data Service for targeted preventive maintenance.